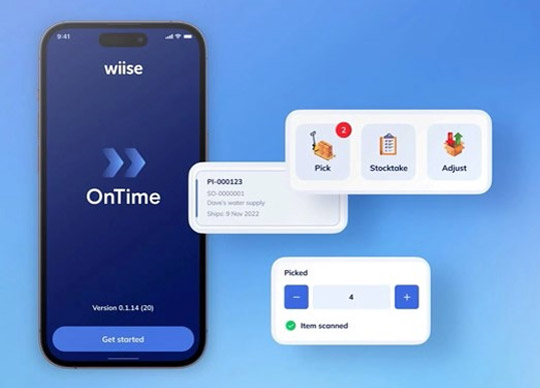
Wiise has announced a new mobile-first warehouse management solution, Warehouse OnTime, to help small and medium-sized businesses manage their inventories and warehouse activities more accurately, and in real-time.
Available for both iOS and Android devices, as well as hardware scanners, Wiise Warehouse OnTime digitises and automates warehouse tasks, removing paperwork and repetitive data entry that often results in mis-picks, delays and errors.
With OnTime, staff can easily receive, pick, put away and adjust stock, as well as complete stocktakes – all from their own device.
The OnTime app speeds up and simplifies warehouse operations, providing customers with:
- Real-time data on warehouse activities and inventory, synched with Wiise’s ERP system
- Mobile access with barcode and QR scanning
- Order prioritising, task filtering and location switching for customers who may have multiple warehouses or locations
- The ability to track the quality of incoming and outgoing goods using the device’s camera, and
- Easy-to-use set up and user-friendly interface, with intuitive navigation and clear instructions
As Australia and New Zealand’s supply chain still grapples with post-pandemic recovery, rising costs and unprecedented competition for warehouse space, the Wiise OnTime app will give inventory-based businesses a real opportunity to modernise operations, meet customer delivery demands and compete with bigger industry players.
Charlie Wood, CEO, Wiise, says Warehouse OnTime will fix critical supply chain gaps, supporting Australian and New Zealand businesses to get customers’ orders to destinations sooner.
“We’re very excited to bring Warehouse OnTime to market – it’s an important step in our commitment to delivering innovative digital solutions to customers, helping them to compete in increasingly challenging times. In the past, smart solutions were only accessible to the largest enterprises, but today’s SaaS, cloud-based systems make technology available to smaller businesses.
Warehouse OnTime increases accuracy and reduces the time it takes to process orders, manage inventory, and onboard staff. It’s particularly powerful for industries such as food, chemical, pharmaceutical or automotive manufacturing and distribution, as it supports serial, lot, and batch tracking – a critical component for recalls, waste reduction and meeting ESG requirements.”
Dunya Lindsey, Chief Product Officer, Wiise, says many of our customers expressed the need to digitise their warehouse processes but couldn’t afford smart warehouse technologies available to bigger businesses.
“Implementing IoT and robotics technology can be expensive, so many businesses still use pen and paper for critical tasks like picking, shipping and stocktakes. Paper-based processes lead to mistakes, which can be costly, from wasted stock through over-buying or unfulfilled sales due to under-buying or delayed orders.