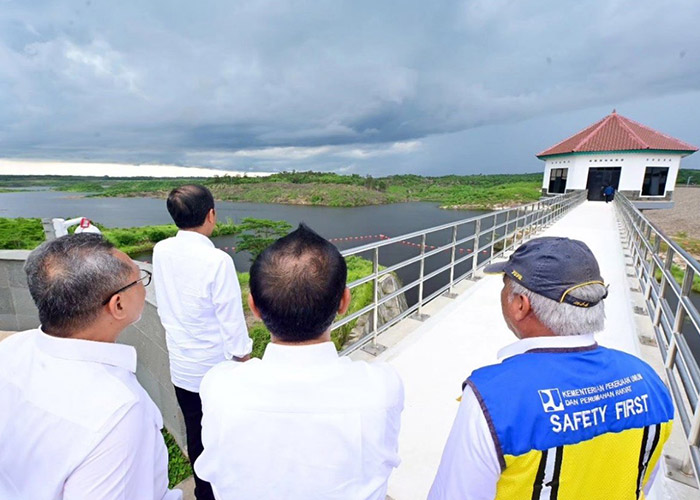
Japanese electronic component and automotive parts manufacturer I-PEX Inc. is adopting Mitsubishi Electric processing machines. By replacing manual grinding activities with a numerically controlled wire electro-discharge grinding process, I-PEX has improved its operations, product quality, and throughput while reducing the number of repetitive tasks for operators.
I-PEX is upgrading its die manufacturing productivity. In line with this, they have installed Mitsubishi Electric’s MP2400 ultra-high precision wire electric discharge machine as a replacement for manual grinding activities.
“About a third of the die manufacturing process relies on Mitsubishi Electric’s technologies,” says I-PEX’s Hajime Kuga. “We heard from Mitsubishi Electric that the MP2400 can reduce the phenomenon of the softening of the machining surface after wire electrolysis to almost zero. After a sample processing test, we got the results we wanted, so we decided to go with this machine.”
The softening of the eroded surface layer of the work piece, a form of electrolytic corrosion, occurs due to the interaction of the processing fluid, de-ionised water, and the direct current used for cutting. However, in the case of the MP2400, electrolysis-free machining is achieved by a high-speed anti-electrolysis power supply.
“Depending on the shape of the piece being worked, it may take more time than machining with a grinder, but the MP2400 can operate unattended overnight, reducing the workload on the operator and potential requirement for overtime,” said Kuga.
In 2020, the company installed a new SV12PM machine, Mitsubishi Electric’s ultra-high-precision die-sinking electric discharge machine. The goal was to increase productivity in manufacturing large dies for automotive parts. “We installed this system based on our in-house findings, indicating that the larger the machining area, the greater the reduction in machining time,” said Kuga. “While this does depend on the size of the die and what is being machined, in our plant, work that took three days to complete with conventional equipment can now be accomplished in two days, and this is a great benefit.”
The MP2400 and SV12PM both utilise Mitsubishi Electric’s iQ Care Remote4U for remote monitoring of operating status and errors. The IPEX team intends to increase automation in the die manufacturing processes through the utilisation of new equipment and services. The close relationship with Mitsubishi Electric is supporting I-PEX’s overall growth strategy.
“While continuing to grow our existing core business of manufacturing electronic and automotive components, we want to expand into new areas, such as the production of piezoelectric MEMS devices that utilise single-crystal films, photoelectric connectors that are crucial for future data centres and telecommunication base stations, as well as healthcare and DNA analysis equipment,” said Kuga.