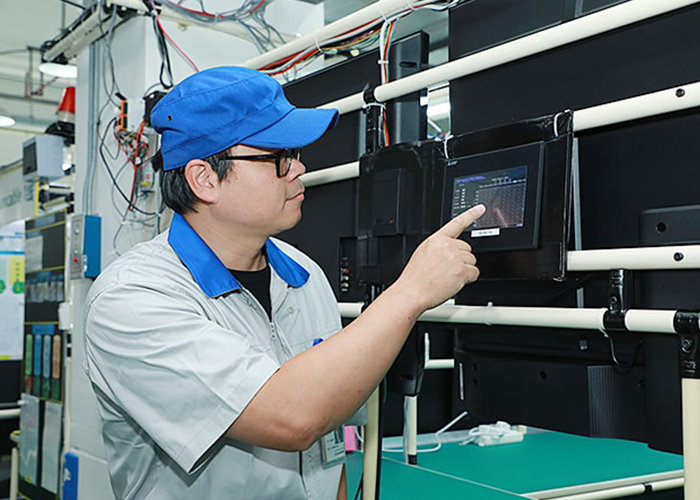
NEC Platform Technologies (Suzhou) Co., Ltd., a Chinese subsidiary of Japan’s NEC Platforms Ltd, has worked with NEC Solution Innovators and Mitsubishi Electric to create a highly efficient picking system utilising PLCs and GOT HMIs.
Technical support and guidance provided by Mitsubishi Electric allowed the company to gain valuable expertise and upgraded the skills of local staff, creating a sustainable system they can continue to expand and develop.
NEC Platforms operates seven facilities in Japan and three internationally, including NEC Platform Technologies in Suzhou. The plant mainly produces routers, with 58 different models being assembled on ten mixed-flow lines that allow production to be changed to meet any fluctuations in demand.
To achieve this level of flexible production, the right parts must be delivered to each line based on the models ordered. On average, 15 components are needed per unit, but the plant uses 450 different parts across 58 router models, and even for the same model, parts may vary depending on the destination market.
Picking the correct parts and delivering them on time is complex, and errors historically caused line stoppages, lowering production efficiency.
NEC Platform Technologies’ Yuhei Fukushima was assigned from the Japanese parent company to oversee production. “I wanted to tackle this issue from a system perspective,” he said.
The challenge arose from a skills gap among local staff. While Fukushima and his team could address picking errors, Japanese staff were only temporarily stationed in Suzhou before returning to Japan. Therefore, relying solely on Japanese engineers wasn’t sustainable. They needed to not only solve the root of the problem, but also to train the local staff to manage the process and any challenges independently.
Fukushima set about introducing digitalisation to the picking process. The result is a system linking work instructions with the shelves where parts are stored. Operators now use a barcode reader to scan a display indicating the model to be produced, which links to a parts database that lists which components are required. LEDs light up to indicate where the corresponding parts are located, making it easy for staff to pick and supply the right parts every time. Mitsubishi Electric’s PLCs, sensors, and GOTs were chosen for the system.
“In Japan, we don’t tend to stick to a single vendor, so I’ve worked with various systems,” said Fukushima, “However, Mitsubishi Electric equipment is always user-friendly. The digitalised picking system has completely eliminated parts supply errors and line stoppages.”
In addition, staffing levels could be reduced by up to 70% while maintaining reduced error rates, allowing reassigned staff to focus on other tasks. Furthermore, the digitalised system has also removed the need for a week-long training program for new staff, a significant advantage in China, where workforce turnover is high.
Another key part of the project was automating the process of transporting parts to the production line after picking. The subsidiary developed its own automated guided vehicle (AGV) using a Mitsubishi Electric PLC for overall control.
Building the AGV in-house reduced costs. “We saw it as a great opportunity to train local staff in technical skills,” said Fukushima. “The AGV’s route can be specified using the GOT’s touchscreen, allowing changes to be made easily without the need for any programming.”
The company also created a system to remotely monitor the temperature and humidity in clean rooms. Previously, a staff member would have to measure and record conditions at ten points inside the clean room. Now, sensors collect this data via a Mitsubishi Electric MES interface unit, which displays it on an external monitor for real-time visualisation. As well as reducing workload, this minimises the need to enter the clean room, helping to maintain the controlled environment.
A key benefit of the project was the ability to pass on valuable technical skills to local staff by developing the systems in-house. Fukushima collaborated with local engineers to program the digitalised picking process, helping to develop their programming skills. Local staff also acquired new automation knowledge through the creation of the AGV and clean room monitoring systems.
“We have built a sustainable system that the local staff can continue to improve and expand themselves,” said Fukushima. “I hope they will take on new challenges, like inventory management linked to ERP or using cameras to analyse issues.”
This project was carried out in partnership with NEC Solution Innovators, a member of Mitsubishi Electric’s e-F@ctory Alliance.