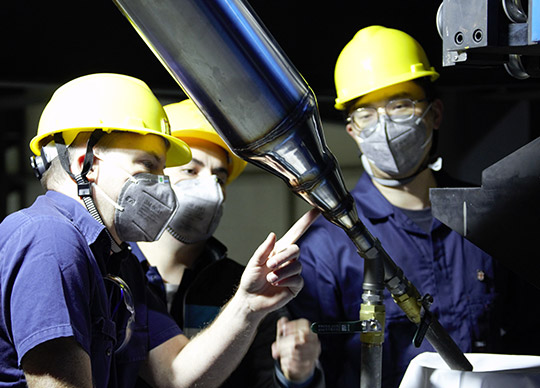
Konica Minolta Australia is assisting the UNSW Materials and Manufacturing Futures Institute (MMFI) at the University of New South Wales (UNSW) address industry needs through the supply and support of 3D printing technology to assist with rapid prototyping and manufacture of end-use products.
The MMFI is studying, building, and transforming the future of materials innovation and advanced manufacturing. It is an interdisciplinary research hub delivering real-world social benefits and tangible solutions to emerging global problems.
Through the MMFI, Australian manufacturers have access to state-of-the-art advanced manufacturing research and problem-solving skills coupled with the technology to address the barriers and opportunities in material sciences and advanced manufacturing, with diverse applications in printed electronics, transport, energy, information technology, and health.
Professor Sean Li, Director, UNSW Material and Manufacturing Futures Institute said, “MMFI has the research expertise and infrastructure to support local industry. It also has access to other skills within UNSW such as science, chemistry, electrical engineering, and medical, providing an even broader skillset that can be tapped. Not only can MMFI come up with a theory, we can use the in-house resources to test that, make changes, and in a short timeframe, produce a practical, real-world solution.”
Matthew Hunter, innovation product marketing manager, Konica Minolta, said, “There is a renewed focus on onshore manufacturing and a massive opportunity for manufacturers in sectors such as aerospace, defence, automotive, and food and beverage. Therefore, it’s critical to have access to resources and skills such as those available through the MMFI to assist with this without requiring massive investment. MMFI has a unique capability to help local industry produce specialised parts that they may previously have had to source offshore.”
The MMFI houses a 3D Systems ProJet HDMax 3500 and a Markforged ProX DMP 300, provided and supported by Konica Minolta. These were both recently used to ensure smooth transfer of graphite powder along the length of a helical screw in a manufacturing line. From prototyping to end-use part, the finished tool was delivered successfully and is now being used to manufacture quality composite materials. From the prompt to the prototype to the product, this whole process was completed within two weeks using the expertise and facilities at the MMFI.
Professor Sean Li said, “MMFI is keen to continue working with diverse industries to provide simple and elegant solutions that meet specific, complex requirements. MMFI has the capability to assist with any step of the process, whether it’s just a concept or ready for the production line. MMFI is committed to helping the industry with the creation of real and useful products, with a balance between commercial, performance, usability, cost, and sustainability.”