
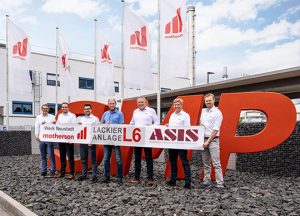
Image caption: Representatives of the ASIS and Motherson project teams at Motherson’s production plant in Neustadt, Germany.
Digital, highly connected, and intelligent, but without overengineering: With the new L6 paint shop, the Motherson company SMP in Neustadt an der Donau, Germany is building a reference plant according to the latest Industry 4.0 standard. Motherson manufactures plastic parts and highly integrated modules for the automotive industry there.
The automatic painting plant is being planned and installed turnkey by ASIS GmbH from Landshut as general contractor. “For more than 22 years a business partnership connects us with SMP. The order for the new L6 is a milestone in the cooperation, which we will deliver in top quality as usual,” says ASIS CEO Hans-Jürgen Multhammer.
Also on board is Wenker GmbH & Co. KG from Ahaus near Münster, Germany, which will supply parts of the plant technology. Due to the high value-added shares of their scope of supply, both partners complement each other extremely well.
Basic Plant Data
In the L6 painting line, plastic parts for the automotive industry are coated high quality. The solvent plant includes the areas pretreatment, water dryer, flaming booth, primer booth, base coat booth, clear coat booth, clear coat dryer, paint supply with high runner systems as well as piggable special paint systems. The application is carried out by robots from the manufacturer ABB. All booths operate in line tracking mode: the product carriers move past the robots while they apply. All robot booths are easily accessible to personnel via a central clean room. A skid conveyor system in combination with lifting and lowering stations moves the workpieces through the three levels of the plant. Assembly will start in the summer of 2022. “Regardless of whether flame treatment, paint supply or application – in all areas we can use our own products, which are already successfully used in many plants. Here we can look back on a great amount of application experience,” says Multhammer.
Solvent vs. Water-based Paint
Since the entry of water-based paints, they have been considered an environmentally friendly alternative to solvent-based paints. At first glance, water-based coatings sound like the greener and therefore better solution. But if you take a closer look at the entire process, including the required plant technology and the associated energy consumption, the situation quickly changes. Compared to solvent systems, water-based coating systems require two additional dryers with associated cooling zones. In addition to the plant costs, this also significantly increases the energy consumption of a water-based painting line. In practice, the exhaust air from water-based coating systems often have to be re-fired with gas, while the solvent concentration in solvent plants is usually sufficient for autothermal operation of the afterburning system. If you calculate the energy requirements of both types of plant, the solvent plant is significantly more energy-efficient than its water-based counterpart. In terms of investment costs, running costs and environmental footprint, the solvent plant is therefore the more sustainable and efficient plant type for the project in Neustadt.
Holistic Simulation
Already during the bidding phase and parallel to the engineering, the calculated throughputs were analyzed in a detailed plant simulation. The holistic approach succeeds by linking general robot simulation with a material flow simulation. Possible bottlenecks were already identified in the design phase and eliminated before construction. Painting plans of the customer are already read in at this stage and simulated with paint-specific parameters, such as color changing times and gaps or part-depending painting times. This powerful tool is then handed out to the customer, who can simulate and verify different process scenarios in advance.
Modern Application
The robots are distributed among the stations flaming, primer, basecoat and clearcoat. Of course, they were also tested in a prior simulation. Nowadays, accessibility studies based on CAD data and meeting the cycle time are a matter of course in plant planning. The CC-Edit (Color Change Edit) software is used to control the track programs. This makes it possible to edit fully automatic color change sequences in complex painting applications and transfer them to the control system. The whole job is done via a graphical user interface and can be implemented quickly and easily even by users with no programming knowledge. The lean software runs on all standard Windows PCs and can also be retrofitted to existing systems.
Digitization
“In the field of digitalization, strong developments are to be expected,” says Stephan Dobmayr, SMP plant manager in Neustadt, “so it is important for us to keep all options open in the future in order to react flexibly and always be state of the art.” The entire control technology of the plant is designed for current, as well as future requirements of digitalization. Smart sensors are installed where possible and useful. Their advantage is that the actual measured value can be continuously output and recorded. Conventional sensors usually only report when the set value is exceeded. The information flows into a central data storage on a database server. The database is pragmatically based on the SQL technology of websites. The majority of all dynamic websites are based on this standard. Data queries are possible device-independent, fast and easy from anywhere in the world. The technology is constantly kept up to the latest IT security standards by a broad community.
Predictive Maintenance
All components that require regular maintenance are equipped with cycle counters and sensors. These count how often a paint valve, pump or motor is actuated. Together with the smart sensors and central data storage, this is the basis for the ASIS Predictive Maintenance module. This is used to calculate in advance when maintenance is required. Components are replaced before they finally break down and the plant comes to a standstill. Process and machine data are analyzed in real time and maintenance recommendations are given. Maintenance can be planned and plant downtimes avoided, while resource use and productivity are optimized and increased.
Process Data Collection
During daily operation, the plant is evaluated and optimized via the Surface Analytics 4.0 process data acquisition. The digital solution provides a global overview of the plant’s performance. Sources of loss are identified and concrete actions are taken. A comparison between different plants is just as possible as over different time periods or between early and late shifts. Whether OEE dashboard, plant availability, energy or media consumption – the reports are attractively presented in interactive diagrams with filter options and automatically sent as monthly or weekly reports by e-mail to defined groups of recipients. Export as PDF, CSV or XLS is also possible. In the skid database, faulty parts can be traced without gaps. Surface Analytics 4.0 can be accessed on all end devices via browser, even on the move, with secure VPN connection. Even the large-format display, for example on large screens in the factory hall to inform and motivate the staff, are further areas of application.
Digitization and Smart Factory is not about rationalizing away jobs. Rather, humans are still essential to operate and change the systems and to recognize and implement intelligent measures. “Designing this human-machine interface in the best easy and intuitive way is what ASIS has made its mission with the claim “Connecting Technology and People”,” explains Multhammer.
Motherson has taken on the challenges of digitalization and is presenting a new showcase plant to the industry with the L6 in Neustadt. There is still a lot to do before the first perfectly coated bumpers roll off the line in the ramp-up phase, but the course is already set for the future.