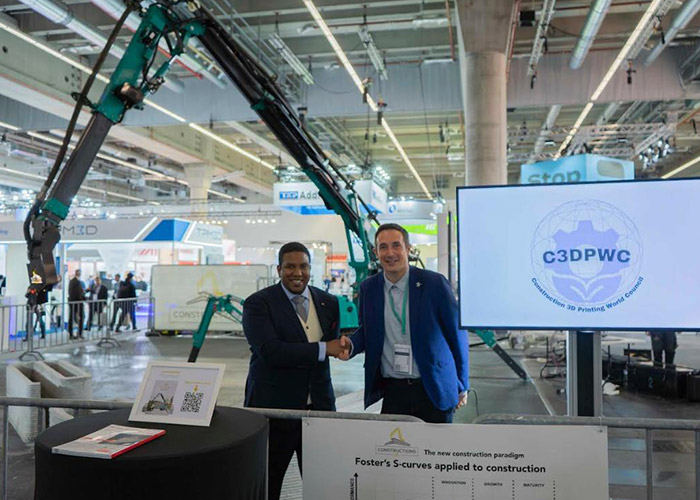
Australian 3D printing technology company Luyten 3D has completed printing a two-storey building in Melbourne, Australia.
“We are extremely proud to become the first-ever 3D printing company in the building and construction sector to deliver on such a monumental achievement. The double-storey building is a two-level granny flat designed to create an instant yet stylish small-format living space,” said Luyten 3D founder and CEO Ahmed Mahil.
The two-storey granny flat was printed in one go at the company’s global headquarters in Melbourne, Australia. Luyten 3D printed the structure using the Platypus X12 printer, the largest printer in its fleet of 3D printers.
The granny flat comprises two bedrooms, a kitchen, a bathroom and a living area. It took 32 hours to build, involving two staff over two and a half day shifts. It is 11 metres wide, 3.2 metres deep and six metres high, including the skillion roof.
The Platypus X12 is the largest mobile AI-powered 3D printer in the world. It is transformative in operation and can convert from a compact size to six metres in height and 12 metres in length, and print using a self-propelled crane which enables it to adjust and move with ease into difficult-to-access spaces and across large sites to print 3D structures.
“To date, building a double-storey structure using 3D printing has been problematic as some firms in the northern hemisphere have only been able to do this by using fixed gantries, which are notoriously expensive to operate and dismantle,” said Mahil. “For those with mobile gantries, they have had to print in separate stages by hoisting up a 3D printer to the second floor or use very expensive repurposed boom trucks which require large areas to operate. In essence, we have solved one of the industry’s biggest challenges – how do we print more than one storey of building in one go.”
Mahil said the granny flat is now a prime example of the benefits of 3D printing for the housing sector, especially in light of the federal government’s affordable housing initiative.
“3D printing can help to ease the building crisis sweeping the country, and the industry needs to embrace 3D printing to galvanise the industry’s long-term future,” he said. “Traditional building methods are proving too costly for an industry that has operated on fixed-cost contracts and archaic building practices. On top of this, labour is becoming scarcer, and building materials are also proving difficult to source, and this is driving up the cost of doing business.”
“3D printing significantly reduces build time and cuts costs for the creation of the structural framework. Rather than laying bricks and building walls, 3D printing simply prints the structure, and trades can then install the final elements.”
Luyten says its 3D printer technology enables builders to undertake construction projects that would traditionally take months or years to complete and instead finish them within days. The 3D concrete printing technology enables a 60% reduction in construction waste, a 70% reduction in production time, and an 80% reduction in labour costs when compared to hands-on construction projects.